Foundry
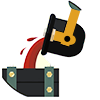
The foundry sector is one of the fastest-growing industrial sectors in India, and one of the most important industries having a bearing on the socio-economic development of the country. There are more than 5,000 foundry units in India, with an installed capacity of approximately 7.5 million tonnes per annum. The Indian foundry sector faces challenges on fronts of energy consumption and environment-friendly technologies. Nevertheless, it has the scope to be more competitive and environment-friendly in its operations for which EE is critical. The project is helping clusters to achieve this by conducting detailed energy audits and introducing new EE technologies in the foundry units.
Clusters
Ahmedabad Foundry Cluster profile
Ahmedabad is located on the banks of river Sabarmati in the state of Gujarat. It is an important industrial cluster in India. Ahmedabad is also one of the largest cities in Gujarat and one of the largest urban agglomerations in India. The industrial activities were developed in mid19th century in this cluster with the setting up of many textile and garment industries. By early 2000s the city had 33 textile mills and was popularly called the ‘Manchester of India’. Subsequently, to support the machinery and spare parts requirements of textile mills, small foundries started being setup in the region.
Process Flow
The major steps in the production process of castings include mould sand preparation, charge preparation, melting, pouring, knockout and finishing. The steps are briefed below :
- Mould sand preparation: Fresh sand is mixed with bentonite and other additives and mixed in muller to make green sand.
- Moulding: The mould sand is pressed by machines or manually on the pattern to prepare the mould. The upper and lower halves of mould are assembled together to prepare the complete mould.
- Charging: Charging is the process of weighing and adding the raw material to furnace for melting. Raw material includes pig iron, scrap, foundry returns and other alloys.
- Melting: The metal charge is melted either in a cupola or induction furnace. The typical temperature requirement is around 1,5000C for CI casting, 1,6500C for steel casting, and 7500C for aluminium casting.
- Pouring: Once the melting is completed, the molten metal is poured into the sand moulds that were prepared in the first stage, using a ladle operated either manually or automatically with the help of cranes. The poured material is then allowed to cooldown and harden.
- Knock-out: After the moulds are left for cooling for the required time, the castings are knocked out from the mould either manually or using a machine.
- Finishing: The finishing operation involves removal of runners/ risers shot blasting and cleaning of the castings.

The foundry industry in Ahmedabad dates back to the 1940s. Since then, a lot of technological improvements have been made in the cluster, especially in melting, sand handling & moulding, and utility sections.
Since Ahmedabad is covered under Phase-I of the GEF-UNIDO-BEE initiative, the energy conservation drive is picking up its pace, and implementations have to be supported under this activity.
Belgaum Foundry Cluster (BFC)
Belgaum Foundry Cluster (BFC) was formed in 2004 with the objective of supporting foundries in Belgaum and nearby areas to enhance their competitiveness, and also for achieving excellence through world class common infrastructure.
As a result of continuous efforts, BFC has set up the following facilities for the benefit of foundries:
1. Optical Emission Spectrometer (OES) for analysing chemical components in metal casting.
2. 3D Coordinate Measuring Machine (CMM) for inspection of casting with high accuracy measuring system.
3. Vertical Machining Centre (VMC) for making patterns, dies and other machining work.
4. Casting simulation, 3D modelling and Enterprise Resource Planning (ERP) software for foundries.
5. Sand reclamation plants for reclaiming thermal sand (2 TPH at 95% reclamation), green sand (10 TPH at 85% reclamation), CO2 /silicate sand (3 TPH at 80% reclamation) and no-bake sand (3 TPH at 85% reclamation).
Overview of Cluster
Belgaum (also known as Belagavi) is one of the old, strong, prominent and cultured historical places nestled high in the Western Ghats in Karnataka. It has an enviable heritage and lies in the zone of cultural transition between Karnataka, Maharashtra, and Goa. Belgaum is also known as the foundry hub of north Karnataka. Belgaum is a pioneer in the development of foundry industrial sector in Karnataka, manufacturing iron & steel castings catering to the needs of General Engineering, Machine Tools, Automobiles, Tractor Components, Pumps, and Motor Body Castings.
The foundry industry in Belgaum has its origins dating back to the 1940s, when the first cupola was set up for manufacturing agricultural implements for local farming community. The industry grew rapidly between 1950 and 1960 with a surge in demand for castings for machine tools, diesel oil engines, electric motors and pump sets. The growth of automobile industry in and around Pune and the setting up of public sector plants such as BHEL and HMT in Bengaluru gave further boost to the demand for castings from the Belgaum cluster.
Belgaum has the presence of more than 150 foundries. Ashok Iron Works is the only large foundry in the cluster and the other units belong to the category of Micro, Small & Medium Enterprises (MSMEs). Foundries in Belgaum cluster are located in five major industrial areas/ estates as follows
Process Flow
The major steps in the production process of castings include mould sand preparation, charge preparation, melting, pouring, knockout and finishing. The steps are briefed below :
- Mould sand preparation: Fresh sand is mixed with bentonite and other additives and mixed in muller to make green sand.
- Moulding: The mould sand is pressed by machines or manually on the pattern to prepare the mould. The upper and lower halves of mould are assembled together to prepare the complete mould.
- Charging: Charging is the process of weighing and adding the raw material to furnace for melting. Raw material includes pig iron, scrap, foundry returns and other alloys.
- Melting: The metal charge is melted either in a cupola or induction furnace. The typical temperature requirement is around 1,5000C for CI casting, 1,6500C for steel casting, and 7500C for aluminium casting.
- Pouring: Once the melting is completed, the molten metal is poured into the sand moulds that were prepared in the first stage, using a ladle operated either manually or automatically with the help of cranes. The poured material is then allowed to cooldown and harden.
- Knock-out: After the moulds are left for cooling for the required time, the castings are knocked out from the mould either manually or using a machine.
- Finishing: The finishing operation involves removal of runners/ risers shot blasting and cleaning of the castings.
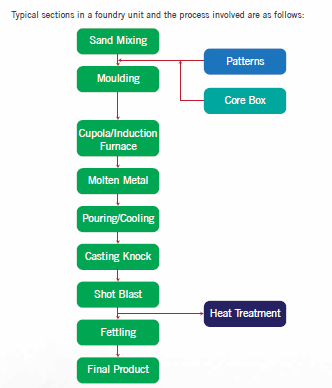
About GEF-UNIDO- BEE project
The project through it various measures has created a real impact on Energy Efficiency in the cluster. Some of the initiatives are as follows: :
- Capacity building workshops for enterprises and local service providers.
- Energy measurement centres.
- Detailed energy audits.
- Identification of technology on Energy Efficiency.
- Financial assistance for demonstration projects.
Howrah
London is the capital city of England.
Coimbatore Foundry Cluster profile
Overview of Cluster
Coimbatore, located in the state of Tamil Nadu, is an important industrial cluster in India. The industrial activities in the cluster developed in the 1930s, with the setting-up of many textiles and spinning units since the local weather was suitable for yarn processing. Initially, the metal casting industry flourished in Coimbatore to cater to the needs of the local textile machinery manufacturers. Subsequently with the start of pump manufacturing in Coimbatore in 1930 and electric motors in 1937, it became an important cluster for manufacture of monoblocs, domestic pumps and subsequently submersible pumps. In 1970s, the wet-grinder was developed in Coimbatore for grinding of rice and lentils used in local recipes. The motor and drive-system of wet-grinders use casting components. Till date, the cluster is by far the largest producer of wet-grinders in India. Subsequently, major automobile manufacturing units like Hyundai, Honda, Leyland, Nissan, LMW and Mahindras have set up auxiliary units to manufacture automobile components. The setting-up of these automobile units created a great demand for castings as well.
Product types and production capacities
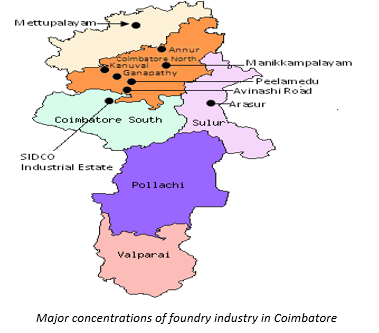
The major raw materials used include base metals (pig iron, steel, borings, scrap and foundry return) and alloys (ferro-silicon, ferro-manganese, iron sulphide, silicon carbide, etc). In addition, small quantities of other metals like copper and tin are added for special grades and SG iron castings.
There are about 535 foundry units in Coimbatore cluster. They are scattered both within and outside the city. Some of the larger foundry units are located in Arasur, Annur, Avinashi Road, Ganapathy, Kanuvai, Manikkampalayam, Mettupalayam, Peelamedu and SIDCO Industrial Estate (Refer the map).
About 15 foundries are of large-scale, 70 in medium scale and others in small and micro category. The production of castings of the cluster is about 2,000 tonne per day (about 0.6 million tonne per annum). The foundry industry employs about 10,000 direct employees and roughly about 25,000 in-direct employees. The estimated turnover of the foundries in the cluster is approximately Rs 3,400 crore per annum.
Several of the foundries in the cluster are of captive type i.e. they produce castings for use in the end-products being manufactured for different end-use applications.
Energy scenario in the cluster
Coke and electricity are the major sources of energy for the foundries. Electricity is sourced from Tamil Nadu Generation and Distribution Corporation Ltd. (TANGEDCO) or from wind farms operating in the southern part of the state. Coke is procured from different distributors. It may be noted that the growth of foundries in the cluster has been adversely affected due to the power shortage in the state. Electricity utilities have put a ceiling of the maximum power demand (called quota demand) that can be used by the industry.
The quota demand has been fixed at 80% of the average demand utilised by the industry during previous year. The industry is required to pay 20% higher tariff if it uses electricity in the peak hours (6 am – 9 am and 6 pm – 10 pm). There is a 5% rebate on the power tariff in the off-peak hours (11 pm – 5 am). Hence most of the foundry units in the cluster are operating in two shifts at present (a) 8 am to 6 pm and (b) and 10 pm to 8 am. The details of major energy sources and tariffs are shown in table.
Table I: Prices of major energy sources

Production process
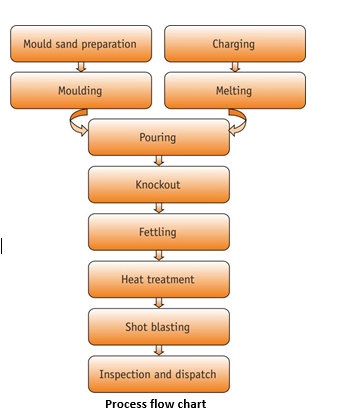
The major steps in the production process of castings include mould sand preparation, charge preparation, melting, pouring, knockout and finishing. The steps are briefed below :
- Mould sand preparation: Fresh sand is mixed with bentonite and other additives and mixed in muller to make green sand.
- Moulding: The mould sand is pressed by machines or manually on the pattern to prepare the mould. The upper and lower halves of mould are assembled together to prepare the complete mould.
- Charging: Charging is the process of weighing and adding the raw material to furnace for melting. Raw material includes pig iron, scrap, foundry returns and other alloys.
- Melting: The metal charge is melted either in a cupola or induction furnace. The typical temperature requirement is around 1,5000C for CI casting, 1,6500C for steel casting, and 7500C for aluminium casting.
- Pouring: Once the melting is completed, the molten metal is poured into the sand moulds that were prepared in the first stage, using a ladle operated either manually or automatically with the help of cranes. The poured material is then allowed to cooldown and harden.
- Knock-out: After the moulds are left for cooling for the required time, the castings are knocked out from the mould either manually or using a machine.
- Finishing: The finishing operation involves removal of runners/ risers shot blasting and cleaning of the castings.
GEF-UNIDO-BEE Project Impact in the cluster
The project through it various measures has created a real impact on Energy Efficiency in the cluster. Some of the initiatives are as follows: :
- Capacity building workshops for enterprises and local service providers.
- Energy measurement centres.
- Detailed energy audits.
- Identification of technology on Energy Efficiency.
- Financial assistance for demonstration projects.