Brass
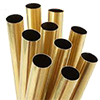
The brass sector is an ever-growing sector in the country with various types of brass-related work units which include brass foundry, brass parts manufacturing, electroplating, extrusion, etc. The units are highly energy-intensive with energy playing a significant role in the overall production costs. Significant potential for savings exists in the sector through adopting EE and RE technologies. The adoption of these technologies can make the units more cost-competitive and sustainable. The project works with the objective of accelerating the adoption of EE & RE technologies and best operating practices in MSME units.
Clusters
Jamnagar Brass Cluster profile
Overview of Cluster
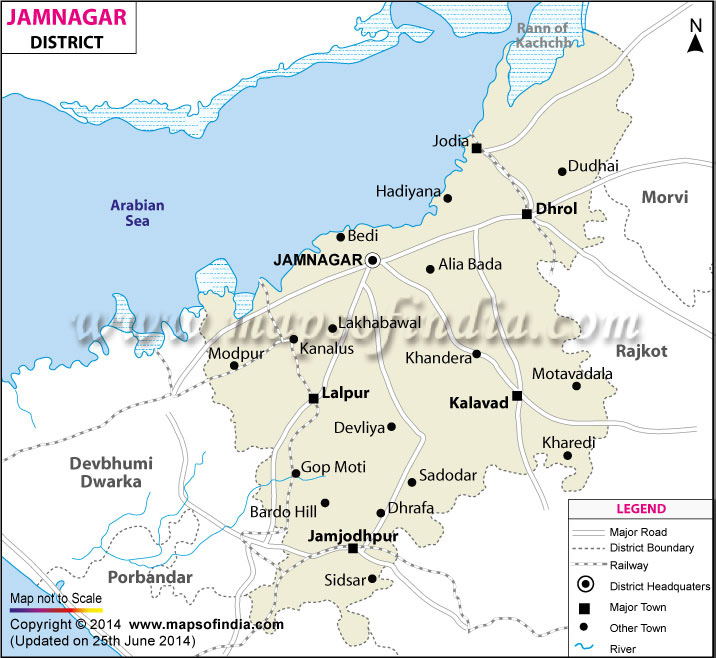
Jamnagar District Is located in the North West of Gujarat State. It is bounded partly by Gulf and partly by the desert of Kutch in the North, Junagadh District in the South, Rajkot District in the East and Arabian Sea in the West. The District has a geographical area of 14,125 sq. km. It is spread between 21.42’ to 22.57’ Latitude and 68.57’ to 70.37’ Longitudes.
Jamnagar is one of the largest brass industry clusters in India. There are around 3,500 brass units in the cluster: 900 foundries, 150 extrusion units, 2,100 machining units, and 350 electroplating units. The units produce between 200–400 tons per annum (tpa). Most of these units have been operating for about 15–20 years. Unlike other brass clusters in India, Jamnagar produces brass products that require extensive machining processes like turning, milling, grinding, drawing, boring, threading, and so on. The brass products from the cluster range from 1 gram to 10 kilogram in weight, and from 0.5 mm to 600 mm in length and diameter.
(Source: www.sameeeksha.org)
Major products manufactured in Jamnagar Brass cluster are:
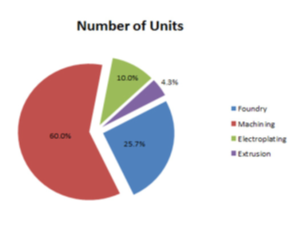
- Building hardware like door & window hinges, stoppers, knobs, studs, handles.
- Brass rods, rounds, hollow rods, square, sections, coils and wire.
- Sanitary & bathroom fittings like venetian blinds, hangers, taps, curtain fittings.
- Electronic & Electrical accessories like socket pin, battery terminal, switches, tester, computer sockets.
- Automobile & Cycle tube valves, industrial control valves.
- Agricultural Implements like tractor accessories.
Process Flow
The production process in the cluster is broadly divided into casting units and extrusion units. While the extrusion units are involved in the production of brass wires; the casting units are involved in manufacturing of a variety of products; some of which are also electroplated, based on the end users’ requirement. Some of the units in the cluster are involved only in machining and electroplating of brass products. The process flow for the two broad categories of units are depicted in the figures below:
There are some units which are involved in production of varied products for which the process flow is modified accordingly.From process point of view, Induction furnace, re-heating furnace, coal pit furnaces are the major energy consuming equipment followed by extrusion press and other machining and lathe machines. The casting units use coal-based pit.
About GEF-UNIDO- BEE project
The project through it various measures has created a real impact on Energy Efficiency in the cluster. Some of the initiatives are as follows: :
- Capacity building workshops for enterprises and local service providers.
- Energy measurement centres.
- Detailed energy audits.
- Identification of technology on Energy Efficiency.
- Financial assistance for demonstration projects.